Introduction to Stainless Steel Factory Production Equipment
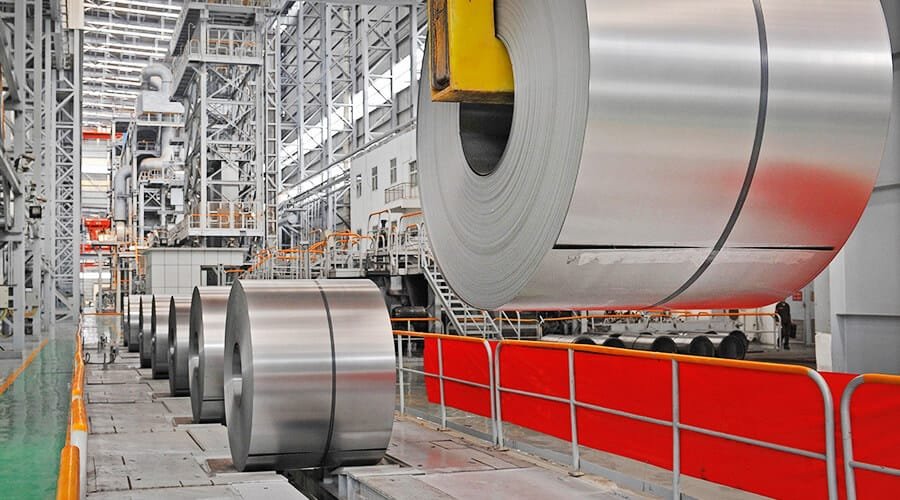
Stainless steel plate production equipment
Electric arc furnace (EAF): used to mix the main raw material alloy iron (chromium iron, nickel iron, etc.) with general steel appropriately, and then melt it by the heat generated by the electric arc.
Refining furnace (AOD or LOD): Roll refining agent into the stainless steel water melted in the electric furnace to remove oxygen, blow in inert gas argon to reduce the carbon and sulfur content, and adjust the chemical composition at the same time.
Continuous casting machine: Equipment for directly making slabs from refined stainless steel water.
Heating furnace: Equipment for heating slabs (blanks) to hot rolling temperature.
Rough rolling furnace: Equipment for producing plate after hot rolling of the blanks heated by the heating furnace.
Finishing mill: Equipment for rolling the stainless steel plate after hot rolling once again to form hot rolled coils and control the final thickness.
Continuous annealing and pickling equipment: Eliminate the hot rolling stress caused by hot rolling and restore the normal metal structure through annealing, pickle the impurities generated during hot rolling, and make the final hot rolled coil.
Surface grinding equipment: For different defects on the surface of products during hot rolling, especially corrosion pits caused by hot rolling continuous annealing and pickling, the surface flatness is adjusted by grinding.
Cold rolling mill: For example, a twenty-roller reversible cold rolling mill is equipped with a full-process automatic thickness control system AGC, which can perform high-precision cold rolling on stainless steel plates to meet different size and performance requirements.
Stainless steel coil production equipment
Reversible cold rolling mill: It can perform high-precision rolling on stainless steel coils to achieve the required thickness and precision. It has a fully automatic plate shape control function and can provide ultra-thin stainless steel coils with precise thickness tolerance.
Glossy annealing furnace: Annealing of cold-rolled stainless steel coils to improve their mechanical properties and surface quality. For example, the vertical annealing furnace imported from Japan adopts a full-line digital control system and advanced sealing design to ensure the perfect quality of the steel strip surface.
Tension leveling machine: The flatness of the leveled steel strip reaches the ideal effect. With an automatic flatness measurement and control system, the stainless steel coil can have a good plate shape.
Slitting machine and transverse shearing machine: mainly used for slitting cold-rolled stainless steel strips, which can be slitting into stainless steel coils of different widths as needed. The slitting machine produced in Taiwan can slitting cold-rolled stainless steel strips with thin thickness and high width accuracy.
Stainless steel pipe production equipment
Pipe making machine: After uncoiling, forming, welding, grinding, sizing, straightening, sizing, cutting and other processes, stainless steel coils or plates are processed into stainless steel pipes.
Shaping equipment: used to shape stainless steel pipes to achieve the specified external dimensions and accuracy. For example, some fast shaping devices can realize automatic shaping of multiple stainless steel pipes at the same time, improving production efficiency.
Polishing equipment: polish the surface of stainless steel pipes to improve their surface finish and aesthetics. Common ones include mechanical polishing equipment, chemical polishing equipment, etc.
Testing equipment: including size detection equipment, non-destructive testing equipment, etc., used to detect the size accuracy, weld quality, surface defects, etc. of stainless steel pipes to ensure that product quality meets the standards. For example, ultrasonic flaw detectors, eddy current detectors, etc.