Stainless steel factories: the solid foundation of modern industry
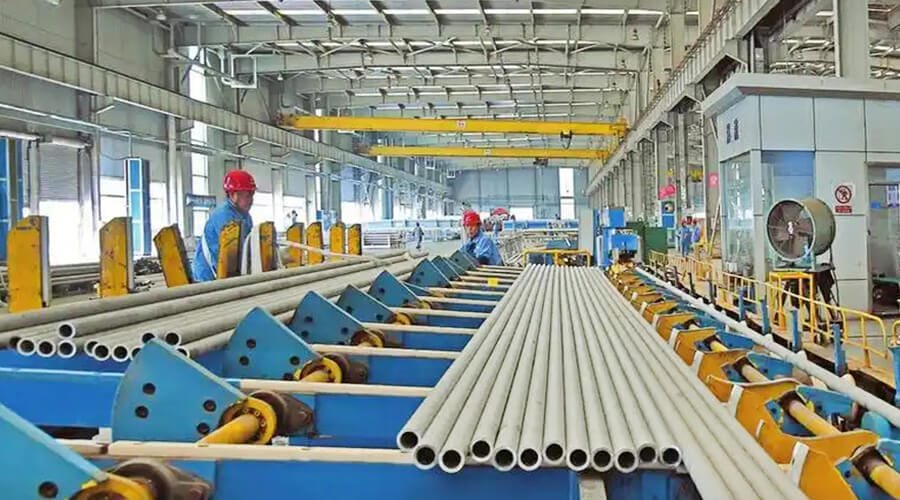
In today’s wave of industrialization, stainless steel factories play a pivotal role. Like the heart of modern industry, they continuously pump out this durable and versatile metal material, supporting the development of many industries.
The production process of stainless steel factories is rigorous and complex. Starting from the selection of raw materials, there are strict standards. The main raw materials such as chromium, nickel, iron, etc. are put into a huge furnace after precise proportioning. Under high temperature, these raw materials gradually merge to form the basic liquid state of stainless steel. Subsequently, through the continuous casting process, the molten steel is poured into a special mold and initially formed into a billet. This billet is then processed into steel plates or steel coils of different thicknesses and specifications through multiple processes such as hot rolling and cold rolling, just like a fine sculpture. Each rolling process requires precise control of pressure and temperature. Any slight deviation may affect the quality of stainless steel.
The product line of stainless steel factories is rich and diverse, which can meet the needs of different fields. There are high-strength stainless steel plates for building structures. With their excellent compression and corrosion resistance, they have become the solid skeleton of high-rise buildings, bridges, etc.; there are also stainless steels for medical devices. Their high purity and biocompatibility ensure the safety and hygiene of medical equipment; and in terms of kitchen supplies, stainless steel has become the preferred material for sinks, pots, etc. with its easy-to-clean and beautiful characteristics.
Quality control is the top priority of stainless steel factories. From the procurement inspection of raw materials, to every process in the production process, to the factory inspection of finished products, the factory has a complete quality monitoring system. The use of advanced testing equipment and technology, such as spectrometers to detect chemical composition and tensile testing machines to test physical properties, ensures that each batch of stainless steel meets strict quality standards, thereby establishing a good reputation in market competition.
The development of stainless steel factories also faces many challenges. Environmental protection is the primary problem. The discharge of wastewater, waste gas and waste residue in the production process puts a certain pressure on the environment. Therefore, factories need to continuously invest in the research and development of environmental protection technologies, such as upgrading sewage treatment systems and installing waste gas purification equipment, to achieve sustainable development. At the same time, as the market’s requirements for the quality and performance of stainless steel products continue to increase, factories must continue to innovate production processes to improve production efficiency and product added value.
In the global economic landscape, stainless steel factories also need to cope with fierce international competition. On the one hand, they need to expand production scale to reduce costs and increase market share; on the other hand, they need to strengthen brand building, enhance the international influence of products, actively expand overseas markets, and compete with internationally renowned steel companies.
In short, stainless steel factories are indispensable in modern industry. With complex production processes, rich product lines, and strict quality control, it provides a solid material foundation for various industries. Although it faces many challenges, as long as it continues to innovate and optimize, it will continue to shine on the industrial stage and contribute a steady stream of “steel power” to global construction and development.